Infrared radiant tube heating systems offer an efficient solution for heating large spaces such as warehouses, factories, and agricultural facilities. Utilizing the principles of radiant heat transfer, these systems provide comfortable and energy-efficient heating, minimizing heat loss and maximizing performance.
Inspired by the Sun
Radiant tube heating systems operate on a principle similar to how the sun heats the Earth. The sun emits electromagnetic radiation, including visible light and infrared rays. When these rays strike the Earth’s surface, they are absorbed and converted into heat, warming the ground and everything on it.
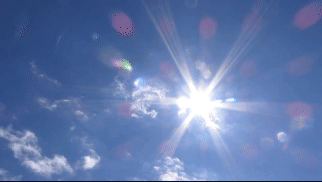
Mid-Infrared Influence
Similarly, radiant tube heaters emit mid-infrared rays that penetrate the air until they encounter an object or mass. Once absorbed by the object, the infrared energy is converted into heat, warming the object and the surrounding air.
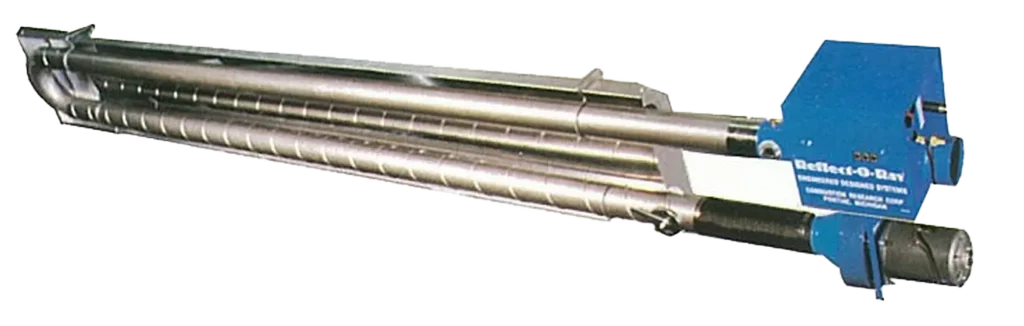
Components of a Radiant Tube Heating System
- Burner:
The heating process starts at the burner, where air and fuel (typically natural gas or propane) mix and ignite to create a flame. - Combustion Tube (Blast Tube):
Directly attached to the burner, this tube is where the flame is contained and the combustion of the air-fuel mixture occurs. It is made from materials capable of withstanding high temperatures, ensuring durability and safety as it carries the hot combustion gases. - Radiant Tube:
Following the combustion tube, this series of tubes carries the hot combustion gases and radiates the heat to the surrounding area. - Hangers and Reflector Shields:
The system is suspended from the ceiling by metal hangers that securely hold both the radiant tubing and the reflector shields. These shields, made of highly reflective metal, focus and guide the radiant energy downwards to maximize heating efficiency. - Exhaust System:
After traveling through the radiant tube, the cooled combustion gases are safely expelled from the system through an exhaust vent.
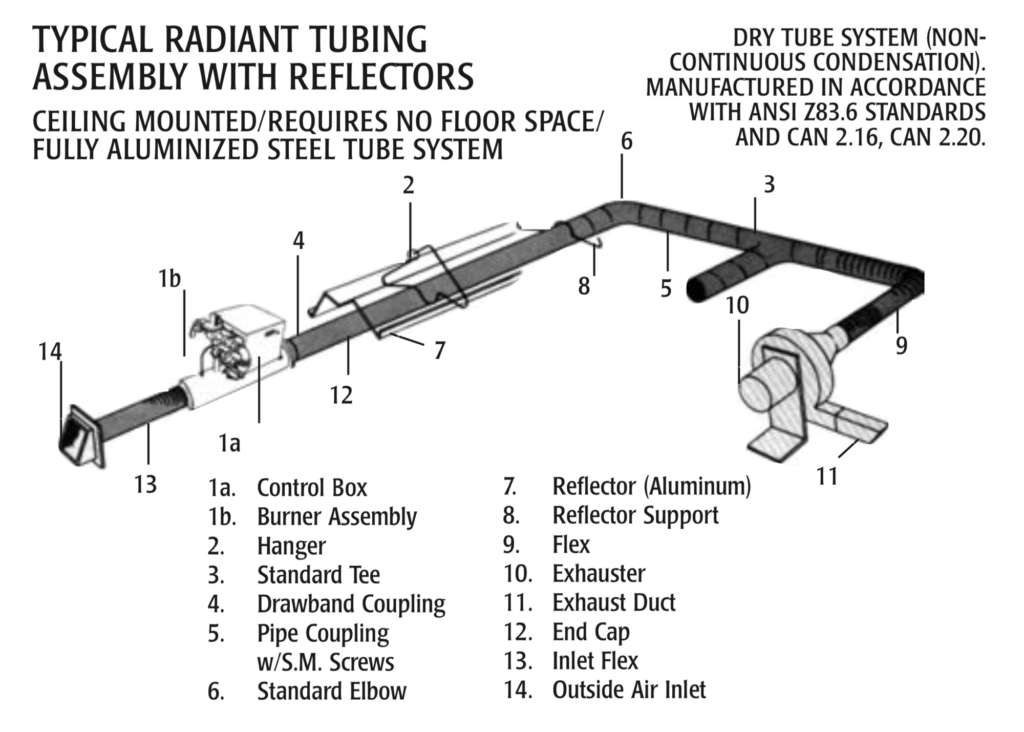
How It Works
- Starting the Burner: The burner ignites, generating hot combustion gases.
- Heat Transfer through the Tubes: The gases flow into a series of connected radiant tubes, which are typically 4 inches in diameter. Some systems may use tubes as small as 3.5 inches or as large as 6 inches, depending on the application.
- Radiating Heat: The tubes emit infrared radiation, warming objects directly in their path.
- Reflecting Heat: Reflector shields direct the infrared energy downward, focusing the heat where it is most needed.
- Heating the Space: Objects that absorb the infrared energy then radiate the heat back into the environment, efficiently warming the space.
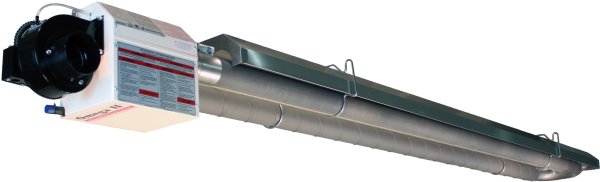
Pressure Systems vs. Vacuum Systems
Radiant tube heating systems can operate under either pressure or vacuum conditions. Pressure systems rely on a blower to push combustion gases through the system but are limited by potential condensation issues in longer tubes. Vacuum systems, on the other hand, use negative pressure to draw combustion gases down the tubes, allowing for longer tube lengths without condensation issues.
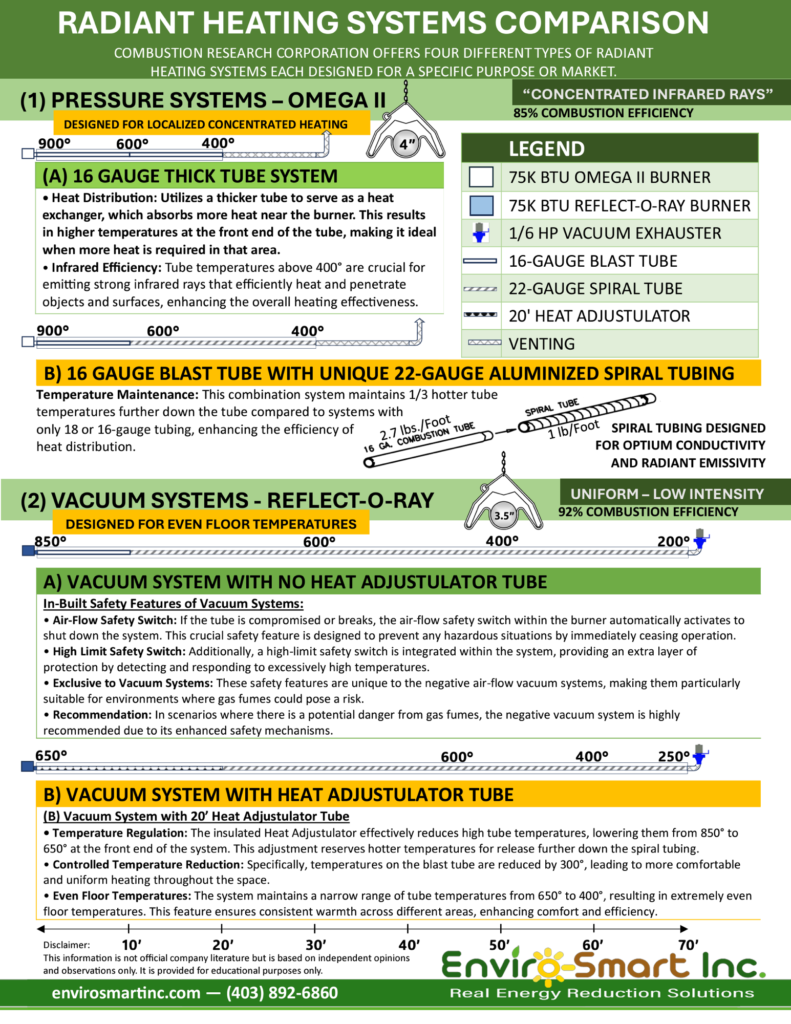
Infrared Radiant Heating Efficiency
The efficiency of a radiant heating system is judged by its ability to warm a space with the least amount of run-time, bringing the space to the desired temperature as quickly and efficiently as possible. Traditional radiant heating systems use heavy 16-gauge black steel for the entire length of the system. This heavy metal construction requires lengthy start-up times before full radiant output is achieved. The heavy black metal also results in uneven room temperatures as these systems have a hard time maintaining high enough tube temperature for full infrared output along the full length of the system. Workers find it uncomfortable to work under the initial segment of the system due to the high intensity and often find not enough heat near the system’s end.
Reflect-O-Ray vacuum and Omega II pressure radiant systems address these inefficiencies by utilizing Combustion Research Corporation’s patented 22-gauge aluminized steel alloy spiral tubing immediately following the blast tube. This lighter, more efficient material allows for quicker heat transfer, resulting in faster start-up times and more uniform radiant output throughout the system. The low mass of this tubing ensures wall-to-wall even temperatures with minimal temperature differentials, typically 1-2 degrees, thanks to its higher emissivity.
This uniform heating is achieved with fewer burners and lower BTU requirements, making Reflect-O-Ray and Omega II systems 30-50% more fuel efficient than traditional all-black metal radiant systems. Thus, not only do these systems heat up more quickly, but they also distribute heat more evenly across large spaces, minimizing energy waste and reducing operational costs. This low intensity heating has been characterized as “soft and non-obtrusive” by end-users. Worker comfort is paramount, productivity increased and maintained.
Conclusion: The Superior Choice in Infrared Radiant Heating
Reflect-O-Ray and Omega II systems exemplify the pinnacle of radiant heating technology. By incorporating advanced design features such as Combustion Research Corporation’s patented 22-gauge aluminized steel alloy spiral tubing, these systems offer significant improvements over traditional models. Not only do they heat up quicker, but they also distribute heat more evenly across large spaces, minimizing energy waste and reducing operational costs.
Whether outfitting a new facility or upgrading an existing one, Reflect-O-Ray and Omega II systems ensure superior comfort and significant savings in energy consumption, proving that innovative engineering can transform how we heat our spaces.