Condensation in buildings is a pervasive issue, often leading to problems like discoloration on garage doors, walls, and ceilings, as well as rust on nails, screws, and door hinges over time. Understanding the causes and consequences of this phenomenon is crucial, and a closer look at underfloor heated facilities reveals significant challenges.
Underfloor Heating and Temperature Differentials
Underfloor heating systems can contribute to uneven temperature differentials within a building. This variation becomes apparent from the floor to walls, and ceiling, creating an environment prone to condensation-related problems. One notable consequence is the visible impact on structural elements like garage doors.
Visible Impact on Structural Elements
In buildings relying on underfloor heating, the drastic floor-to-wall temperature differentials can result in discoloration on garage doors due to condensation. This occurs when the warm, moist air near the floor meets the colder surfaces of the garage door. Over time, this moisture can lead to unsightly discoloration, affecting the aesthetic appeal of the building.
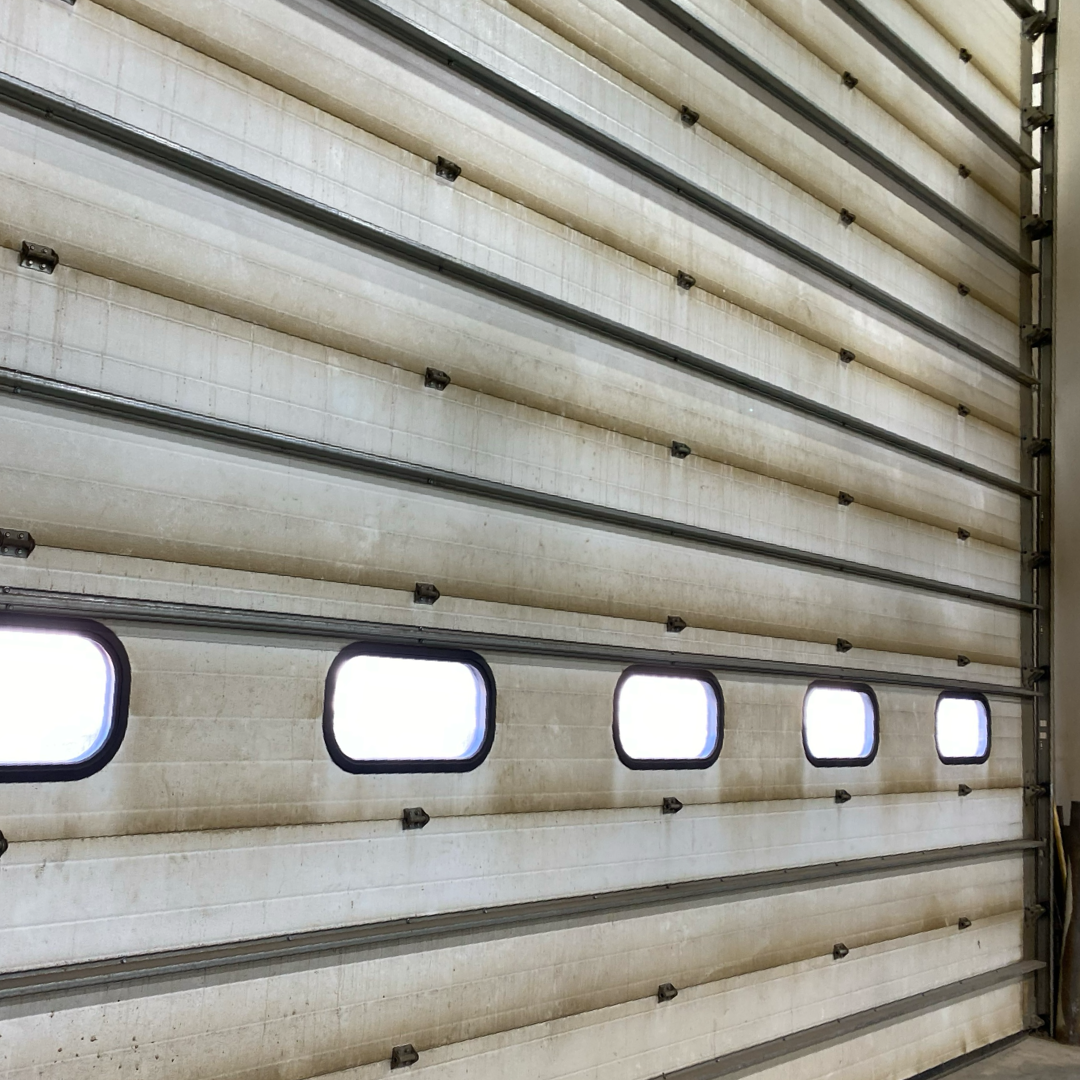
Rust Formation and Structural Degradation
Furthermore, the temperature differentials in underfloor heated buildings can contribute to rust formation on bolts nails, screws, and door hinges. The condensation that arises from varying temperatures can accelerate the oxidation process, leading to structural degradation over time.
The LED Lighting Factor
The shift to LED lighting, driven by energy efficiency, has also brought with it unforeseen consequences. LED lights, while excelling in cost-effectiveness, lack the warming element that characterized their halogen counterparts. This shift introduces a dynamic where rising warm air now encounters cooler ceilings, setting the stage for condensation-related challenges.
The collision of rising warm air and a cooler ceiling, manifests visually as discoloration. Ceilings that were once protected by the warmth of halogen lights now contend with an environment conducive to moisture accumulation and the subsequent discoloration.
In the era of halogen and incandescent lighting, shop owners didn’t realize that the fixtures shining down were unintentionally acting as mini electric radiant heaters. The radiant warmth served as an unintended shield, keeping condensation issues at bay on ceilings.
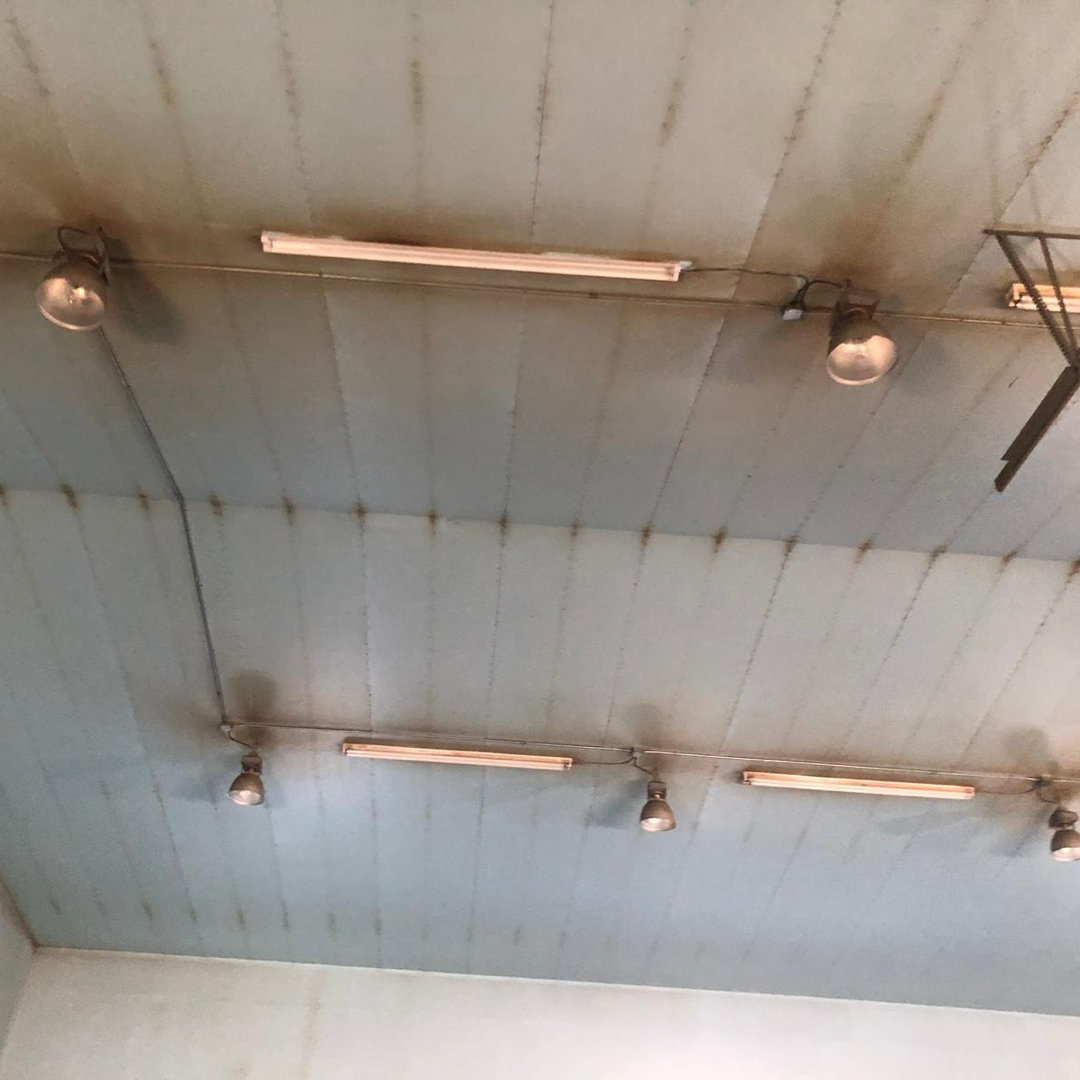
Reflect-O-Ray® as a Preventive Solution
Reflect-O-Ray® emerges as a preventive solution to these challenges. Its ability to provide even heat distribution with minimal temperature differentials sets it apart. Reflect-O-Ray® ensures a mere 1-2 degree temperature differentials, creating an environment where condensation-related issues are eliminated.
Preserving Structural Integrity and Appearance
Garage doors, walls, and ceilings remain unaffected by the temperature variations that typically plague underfloor heated facilities. With Reflect-O-Ray®’s innovative design, which focuses on efficient and consistent radiant heating, the risk of condensation-related problems is mitigated, preserving the structural integrity and appearance of buildings.
Conclusion
In summary, the concern of condensation in buildings, especially those with underfloor heating, highlights significant challenges with both visible and structural implications. Facilities benefiting from an Engineered Designed Reflect-O-Ray® system, such as EDS 4.0 or EDS 3.5, enjoy consistent heat distribution and minimal temperature variations, effectively mitigating condensation-related issues. This strategic approach to creating a comfortable and well-maintained indoor environment establishes Reflect-O-Ray® as the smart solution for preserving both structural integrity and aesthetic appeal.